ASR Mitigation with Pumice-Blended Cement
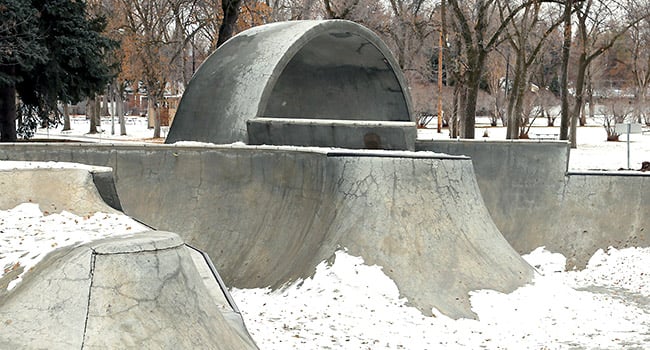
ABOVE: This public skate park in Idaho Falls, an area known for its reactive aggregate, is being slowly and relentlessly destroyed by ASR. BELOW: Close up of the ASR-infected concrete.
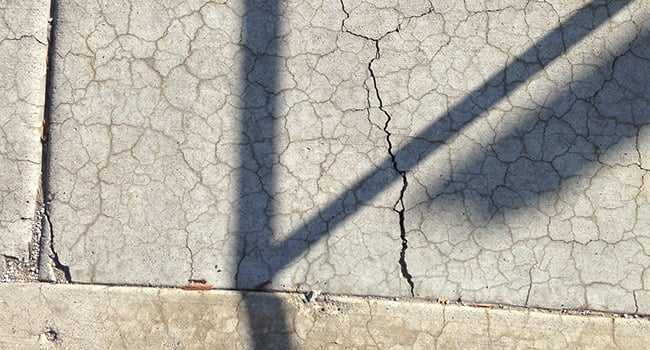
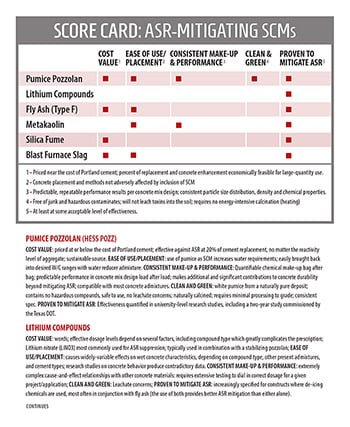
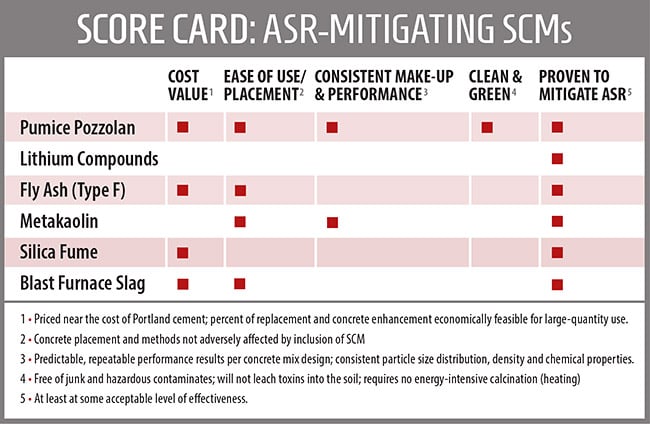
PDF document—Score Card: ASR-Mitigating SCMs—details how pumice pozzolan stacks up against various supplementary cementitious materials used to mitigate the alkali-silica reaction.
ALKALI-SILICA REACTION (ASR) fuels a relentless, slow-motion explosion within cured concrete that shatters both the concrete and the aggregate, significantly shortening the engineered lifespan of the infected structure.
On most lists that bullet-point top contributors to premature concrete failure, ASR is second only to corrosion of reinforcing steel. The irony in that one-two list relationship is the fact that even mild ASR-fueled map-cracking accelerates the chemical attacks on reinforcing steel.
Once the alkali-silica reaction kindles within concrete—triggered by the collision of alkali, silica, moisture, and unconverted calcium hydroxide (a deleterious byproduct spawned by the Portland cement+ water hydration reaction)—it cannot be stopped. Failure is imminent.
The solution? Mitigate ASR in the concrete mix design.
The ASR Train Wreck Explained
Researchers have defined a causal triangle that sets off the chemical ASR train wreck within concrete. The stew of water, Portland cement, and reactive aggregate generate the four essential ingredients of expansive ASR gel—alkalis, silica, free calcium hydroxide (CH), and moisture. Starving the concrete of one of those components can effectively flatline ASR.
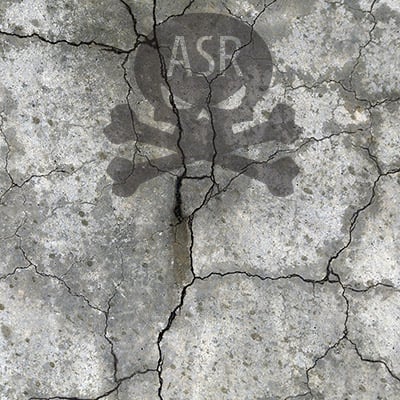
Simple Explanation: the alkali compounds within Portland cement react with the silica in the aggregate forming a chemical compound with a thirsty affinity for water. As water is absorbed, the resulting gel swells, cracking both concrete and aggregate, opening the concrete to further attack from outside elements—sulfates and chlorides, marine salts, and freeze-thaw—which accelerate the death-march of the structure.
Deep Dive: the primary chemical reaction (hydration) between Portland cement and water creates a deleterious compound know as Calcium Hydroxide (CH)—radical free calcium—that, unabated, reacts with alkali and aggregate-contributed silica to form a hydrophilic (water-attracting) gel that expands relentlessly. The reaction will go dormant when starved of moisture, only to swell and expand again when sufficient water is again present.
In many cases, several concrete-destroying mechanisms are acting together. Some of the deleterious CH also migrates to the surface, leaving behind a porous network of microscopic, inter-connected wormholes that provide for easy ingress of water to continue to fuel the expansive ASR gel. Free ingress of water also begins the destructive freeze-thaw cycle. Chlorides and sulfates also join the invasion, attacking the concrete and the reinforcing steel within. As ASR-induced map-cracking spreads to the surface, the death-march of the structure is accelerated.
Once the alkali-silica reaction begins within placed concrete, it cannot be stopped. Several methods are effective in slowing it down—(various drying methods, chemical treatments, stress relief, restraint)—but the hard facts are these: ASR-affected concrete is flawed at the molecular level and will not reach its engineered lifespan.
Defeating ASR
Where concrete engineers have had success combating and defeating ASR is with preventative mix designs. Various ineffective and often impractical methods have been identified and used since the alkali-silica reaction was first identified in the late 1930s, including using low-alkali cement, trucking in non-reactive aggregate, specifying low W/C ratios, using less cement, even air entrainment.
Until now, the most effective and practical solutions involved using SCMs that in one way or another disrupted the corruptive union of alkali, silica, moisture, and CH. These SCMs included lithium nitrate, Metakaolin, silica fume, flash-cooled furnace slag, and a combination of low-alkali cement and Class F fly ash.
Recent research, spurred by studies made on enduring Roman concrete structures (many over 2000 years old), has centered on the use of pumice as an excellent SCM for improving modern concrete performance and lifespan. This historical evidence, combined with current, quantifiable research, has also revealed pumice to be a particularly effective mitigator of ASR.
Pumice is a natural SCM mined and refined from the Hess deposit in southeast Idaho: the world’s purest commercial deposit of white pumice. Pumice doesn’t need calcining in an energy-intensive fiery furnace; it is not a befouled by-product of some industrial process. It’s a simple product with a complex chemical nature that powers a welcome reaction within hydrated concrete that flatlines the alkali-silica reaction.
LINKED RESOURCES
—Download a Summary of the Pumice Pozzolan Research (including the effectiveness of pumice pozzolan to flatline ASR) from the University of Texas-Austin and the University of Utah.
—Download the Whitepaper: Flatline ASR With Pumice-Blended Cement.
—Download the Knowledge Brief: Score Card: ASR-Mitigating SCMs.
—Visit the ASR MitiGator website.